|
 |

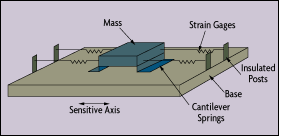 |
Figure 6-3: Early Mechanical Vibration Sensor
|
Acceleration & Vibration
Early acceleration and vibration sensors were complex mechanical contraptions (Figure 6-3) and were better suited for the laboratory than the plant floor. Modern accelerometers, however, have benefited from the advance of technology: their cost, accuracy, and ease of use all have improved over the years.
Early accelerometers were analog electronic devices that were later converted into digital electronic and microprocessor-based designs. The air-bag controls of the automobile industry use hybrid micro-electromechanical systems (MEMS). These devices rely on what was once considered a flaw in semiconductor design: a "released layer" or loose piece of circuit material in the microspace above the chip surface. In a digital circuit, this loose layer interferes with the smooth flow of electrons, because it reacts with the surrounding analog environment.
In a MEMS accelerometer, this loose layer is used as a sensor to measure acceleration. In today's autos, MEMS sensors are used in air bag and chassis control, in side-impact detection and in antilock braking systems. Auto industry acceleration sensors are available for frequencies from 0.1 to 1,500 Hz, with dynamic ranges of 1.5 to 250 G around 1 or 2 axes, and with sensitivities of 7.62 to 1333 mV/G.
Industrial applications for accelerometers include machinery vibration monitoring to diagnose, for example, out-of-balance conditions of rotating parts. An accelerometer-based vibration analyzer can detect abnormal vibrations, analyze the vibration signature, and help identify its cause.
Another application is structural testing, where the presence of a structural defect, such as a crack, bad weld, or corrosion can change the vibration signature of a structure. The structure may be the casing of a motor or turbine, a reactor vessel, or a tank. The test is performed by striking the structure with a hammer, exciting the structure with a known forcing function. This generates a vibration pattern that can be recorded, analyzed, and compared to a reference signature.
Acceleration sensors also play a role in orientation and direction-finding. In such applications, miniature triaxial sensors detect changes in roll, pitch, and azimuth (angle of horizontal deviation), or X, Y, and Z axes. Such sensors can be used to track drill bits in drilling operations, determine orientation for buoys and sonar systems, serve as compasses, and replace gyroscopes in inertial navigation systems.
Mechanical accelerometers, such as the seismic mass accelerometer, velocity sensor, and the mechanical magnetic switch, detect the force imposed on a mass when acceleration occurs. The mass resists the force of acceleration and thereby causes a deflection or a physical displacement, which can be measured by proximity detectors or strain gages (Figure 6-3). Many of these sensors are equipped with dampening devices such as springs or magnets to prevent oscillation.
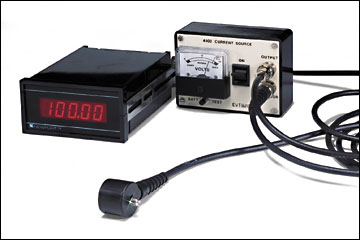 |
Industrial accelerometer with associated electronics.
|
A servo accelerometer, for example, measures accelerations from 1 microG to more than 50 G. It uses a rotating mechanism that is intentionally imbalanced in its plane of rotation. When acceleration occurs, it causes an angular movement that can be sensed by a proximity detector.
Among the newer mechanical accelerometer designs is the thermal accelerometer: This sensor detects position through heat transfer. A seismic mass is positioned above a heat source. If the mass moves because of acceleration, the proximity to the heat source changes and the temperature of the mass changes. Polysilicon thermopiles are used to detect changes in temperature.
In capacitance sensing accelerometers, micromachined capacitive plates (CMOS capacitor plates only 60 microns deep) form a mass of about 50 micrograms. As acceleration deforms the plates, a measurable change in capacitance results. But piezoelectric accelerometers are perhaps the most practical devices for measuring shock and vibration. Similar to a mechanical sensor, this device includes a mass that, when accelerated, exerts an inertial force on a piezoelectric crystal.
In high temperature applications where it is difficult to install microelectronics within the sensor, high impedance devices can be used. Here, the leads from the crystal sensor are connected to a high gain amplifier. The output, which is proportional to the force of acceleration, is then read by the high gain amplifier. Where temperature is not excessive, low impedance microelectronics can be embedded in the sensor to detect the voltages generated by the crystals. Both high and low impedance designs can be mechanically connected to the structure's surface, or secured to it by adhesives or magnetic means. These piezoelectric sensors are suited for the measurement of short durations of acceleration only.
Piezoresistive and strain gage sensors operate in a similar fashion, but strain gage elements are temperature sensitive and require compensation. They are preferred for low frequency vibration, long-duration shock, and constant acceleration applications. Piezoresistive units are rugged, and can operate at frequencies up to 2,000 Hz.
|